Our New Product Introduction Manager, Simon Lester has been featured in this month’s Irrigation Leader magazine, you can read the article, below!
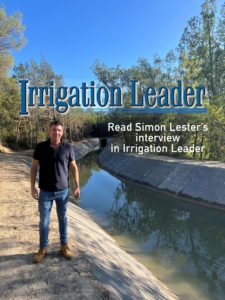
Concrete Canvas has a new solution to eliminate seepage loss: a flexible, concrete-filled fabric that hardens on hydration to form a thin, durable, waterproof, and lower-carbon concrete layer. In this interview, Simon Lester, Concrete Canvas’s new product introduction manager, introduces CCX, the company’s next-generation roll-it, lay-it, and spray-it solution that allows customers to line their own canal or ditch in a day.
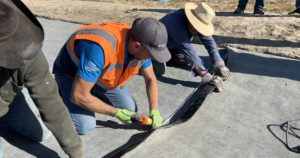
Irrigation Leader: Please tell us about your background and how you came to be in your current position.
Simon Lester: I was born in Cape Town, South Africa, where my father worked as an accountant for 50 years. Having attended school and university in South Africa, I got my undergraduate in psychology and geography. I then spent a couple of years traveling overseas, teaching English in Taiwan and backpacking through Southeast Asia. While backpacking, I decided to go back to university to get a civil engineering degree. After graduating in 2005, I went into construction, working predominantly on concrete structures for highways in Swaziland. In 2010, I was looking for an alternative for a canal lining project we were bidding on in Swaziland when I came across an advertisement for Concrete Canvas. I flew to the UK and met William Crawford and Peter Brewin, the inventors and owners of Concrete Canvas. I immediately fell in love with the product and became a distributor for Malawi, Mozambique, Swaziland, and Zambia.
At this stage, I was focusing predominantly on using Concrete Canvas for the lining of irrigation canals on sugar estates. These estates had a mixture of unlined and geomembrane- or concrete-lined canals. Working with these clients on a number of initial projects provided me with the opportunity to understand the requirements and challenges irrigators face on a day-to-day basis. In those days, Concrete Canvas was a new technology in Africa as well as globally, so competing with traditional lining techniques in the irrigation sector was tough. It didn’t work out at that stage, but I stayed affiliated with Concrete Canvas, and in 2015, Mr.Crawford and Mr.Brewin offered me a job as the business development manager for subSaharan Africa. I started that role in 2016 and have been with the company ever since. In 2020, I took on my current role as new product introduction manager for CCX, our next-generation product, and I emigrated to the UK with my wife and three sons to take up a position at our head office just outside Cardiff in Wales.
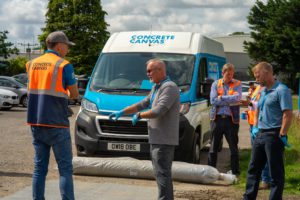
Irrigation Leader: Please introduce Concrete Canvas.
Simon Lester: Concrete Canvas was developed out of a master’s thesis by William Crawford and Peter Brewin. They were looking for a cementitious product that essentially mimicked the performance of a plaster of Paris bandage. Initially, Concrete Canvas was used to create rapidly deployable inflatable shelters that could be used in war-torn or disaster-stricken areas. The shelters were designed to be inflated and then sprayed with a Concrete Canvas surface that cured in position. Within 24 hours, they were habitable. Mr. Crawford and Mr. Brewin quickly realized, though, that the shelter skin had much greater potential in erosion-control applications such as lining ditches and protecting slopes. In 2009, Concrete Canvas became commercially available on an industrial scale. It was initially manufactured in Pontypridd, in South Wales, but as demand has grown, we’ve had to increase production capacity, resulting in a move to our current premises in Pontyclun. Today, nearly 90 percent of our products are exported around the world to some 80 countries. Our core applications are ditch and canal lining, slope protection, the remediation of existing concrete infrastructure, weed suppression, and secondary containment applications.
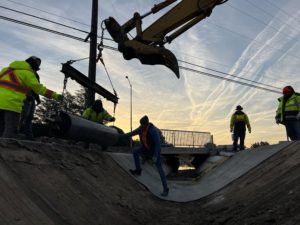
Irrigation Leader: How long have you been operating in the United States?
Simon Lester: Our U.S. company officially opened in Houston in 2021. We used to operate on a purely distribution basis, with several distributors across the country covering different territories and sectors. Melanie Fuhrman is the general manager of Concrete Canvas USA and heads up a great in-country team covering sales, technical matters, and logistics.
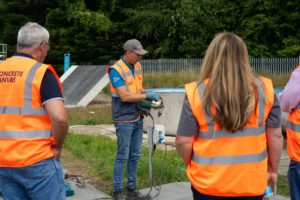
Irrigation Leader: Please tell us about your CCX products.
Simon Lester: Concrete Canvas is a flexible, concrete-filled fabric that hardens on hydration to form a durable, waterproof concrete layer. The concrete hard-armoring provides the strength and protection functionality, while the geomembrane backing provides the waterproofing functionality. The product that we predominantly use for lining canals in irrigation applications is called CCX. In one application, it provides what would typically require multiple products or component applications in the field. This is fundamental to a lot of our clients, especially in the irrigation sector, because they have limited time during the off-season to implement a lining solution or remediate existing canals. The product comes in a prefabricated roll. You pull it off the roll, lay it, cut it with a utility knife or rotary cutter, fix it place, and spray it with water. Within a day, you have a usable lining solution. It’s quick and simple to install, and it doesn’t require skilled labor, allowing most irrigators the option to do it themselves. CCX has a minimum lifespan of 50 years and is cost competitive with traditional lining solutions.
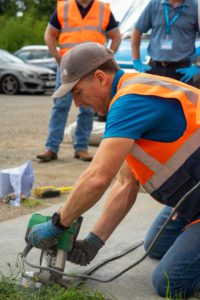
Irrigation Leader: How thick is CCX?
Simon Lester: CCX-M, used for canal lining, is 0.4 inches thick, with the addition of a 12-mil linear low-density polyethylene geomembrane backing. CCX-M is typically used to replace 2–4 inches of cast-in-situ concrete, shotcrete, or precast concrete elements, with or without a geomembrane underlay. The stock roll length is 164 feet long by 6.3 feet wide, equating to approximately 1,000 square feet per roll.
Irrigation Leader: Please tell us about your pilot projects in irrigation districts around the western United States.
Simon Lester: The western United States, like many places around the world, is facing acute water shortages. It is becoming critical to mitigate water seepage, which, in addition to reducing water supply and revenue, can cause waterlogging, increase the salinity of adjacent soils, or pose risks to infrastructure next to canals. We’ve just completed pilot projects for irrigation districts in California, Colorado, Nebraska, and Washington aimed at eliminating these issues. For example, in California, we completed the lining of a lateral canal that was approximately 1,500 feet long and 16 feet wide in less than 4 days. The CCX-M joints were thermally bonded to provide a low-permeability lining solution. A pond test was then conducted, and based on the measured seepage losses, the client has expressed their satisfaction with the performance of the pilot and is now considering Concrete Canvas as an alternative to their current solutions.
Irrigation Leader: What should every irrigation district know about Concrete Canvas?
Simon Lester: Concrete Canvas is a rapid, cost-effective, lower-carbon, and longer-lasting alternative to conventional liners and has variants designed specifically for the lining of irrigation canals. It allows irrigation districts to conserve water, reduce installation and maintenance costs, and self-perform. We are well positioned in the United States and globally to support irrigators and ensure successful project execution.
Irrigation Leader Magazine is available here.